THE FUTURE OF X-RAYS: FROM RADIOGENIC TUBES VS NANOTUBES - WHAT DOES TECHNOLOGY HOLD?
Pubblicato da Brigida Michele in Xrayconsult · Venerdì 13 Ott 2023
Tags: BLOG, Emissione, di, campo, Elettroni, Programmabilità, Materiali, CNT
Tags: BLOG, Emissione, di, campo, Elettroni, Programmabilità, Materiali, CNT
THE FUTURE OF X-RAYS:
FROM RADIOGENIC TUBES VS NANOTUBES
WHAT DOES TECHNOLOGY HOLD?
Historical Introduction and Investigation
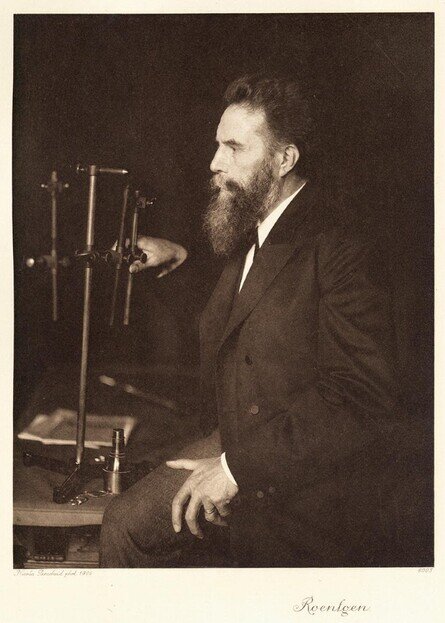
"Professor. Dr. Wilhelm Conrad Roentgen"
History of the Discovery of X-raysIn January 1897, after a year of discoveries and challenges, Conrad Roentgen confessed to his friend Zehnder his temporary renunciation of working with X-ray tubes, calling them more unpredictable than women.This decision was preceded by an extraordinary discovery in the autumn of 1895.Wilhelm Conrad Roentgen, the professor doctor, pictured in his laboratory in 1897, was experimenting with vacuum glass tubes and large Ruhmkorff inductors.On a dark autumn evening in Würzburg, he noticed a glow on a cardboard sheet coated with barium tetracyanoplatinate.This screen was originally intended to visualize cathode rays and ultraviolet light.Surprisingly, the glow persisted despite measures taken to turn it off, and Roentgen discovered that objects placed in front of the tube did not completely obscure it.The subsequent discovery revealed that these mysterious "X-rays" were generated by the tube itself, interacting with the glass and metal targets inside the envelope.Roentgen developed the magnetic deflection of the focal spot, an innovation used in modern computed tomography.The shadows of objects became visible on a screen when the gas in the tube was active, with the correct pressure and voltage. Their intensity decreased with distance from the glass wall.In short, Roentgen made a revolutionary discovery, paving the way for medical radiography and the understanding of X-rays.The patent for the X-ray tube is attributed to William David Coolidge, an American physicist and electrical engineer. Coolidge developed the X-ray tube in the first decade of the 20th century and was granted a patent for it in 1913.This type of vacuum tube is used for the production of X-rays and has been a fundamental part in the development of medical radiography and other applications involving X-rays."Coolidge's 1916 patent for GE, a thermionic tungsten emitter"Brief overview of the experiment and components used:Conrad Roentgen conducted pioneering experiments on the generation of X-rays using a Crookes-style tube.To evacuate the tube to a residual pressure of about 10 Pa, he used a Raps automatic mercury pump, powered by tap water.A Ruhmkorff induction coil generated a voltage of a few dozen kilovolts peak, alternating at 10-15 Hz, adjusted by a spark gap about 3 cm wide.Inside the tube, electrons were released in a gas discharge and then bombarded the aluminum cathode, charged to a high negative potential, generating X-rays in the glass wall on the right.![]()
"The X-ray tube used by Conrad Roentgen"An anticathode positioned at the top right served to repel scattered electrons, while it was crucial that the glass wall showed greenish fluorescence when hit by the electrons.Precise regulation of the gas pressure required experience, as too high or too low a pressure would compromise the tube's operation.When ionization decreased, the high voltage increased, often leading to external discharges that damaged the glass.Roentgen used numerous tubes during the early stages of his research, but only one survived.These tubes were crucial tools for his revolutionary discovery of X-rays, achieved through rigorously planned experiments conducted with great skill.In summary, Roentgen used a vacuum tube with an inductor to generate X-rays, paying attention to the regulation of the gas pressure, despite the frequent consumption of such devices during his research."Laboratory with Ruhmkorff Inductor connected to a Crookes tube"The beginning of industrial productionIn February 1896, Hermann Kuemmell, a chief surgeon at the University Hospital of Hamburg-Eppendorf, Germany, inspired by newspaper articles about the discovery of X-rays, insisted on purchasing an X-ray machine.This decision was enthusiastically discussed by his team, although it was still surrounded by disbelief.Kuemmell sent two of his assistants to the glassblowing workshop of CHF Mueller in Hamburg, where a wide range of equipment, including thermionic tubes, was being produced for scientific and lighting purposes.Mueller began experimenting with X-rays, with the aim of improving the quality of X-ray tubes."Glassblowing workshop of CHF Mueller, 1920s"After some delays, on March 20, 1896, X-rays were used clinically for the first time at the University Hospital of Hamburg.Less than a week later, on March 26, 1896, Siemens and Halske filed the first patent for an X-ray tube.Mueller played a key role in the development of X-ray tubes, making improvements such as converting the cathode into a concave mirror and coating the anticathode with platinum.The Mueller company evolved over the years to become a leader in medical imaging systems technology and celebrated its 100,000th tube in 1911. In 1927, it was acquired by Philips."Image of the CHF Mueller price list from 1880"Conventional X-ray TubeX-ray tubes generate X-rays by accelerating electrons through a high-voltage electric field and then rapidly stopping the high-speed electrons with a dense metal.When the high-speed electrons lose energy, some of that energy becomes X-rays.Conventional X-ray tubes create electrons in the tube thermionically by boiling them off a thin tungsten filament.A current of electrons is passed through the thin filament, similar to an incandescent light bulb, and the filament heats up to 1400°C. As the filament gets hotter, more electrons will be generated.These electrons are generated from the atoms of the filament and over time, the filament will exhaust its material and burn out.This is called thermionic emission.Below we see some of the most common and used tubes in different sectors, both externally and the internal section designed.![]()
" Rotating anode tube" "Stationary anode tube" "Enclosed tube"![]()
"X-ray Tubes Currently Used in Various Sectors""Major Manufacturers with the Most Significant Improvements"X-rays are used in a variety of sectors for diagnostic, inspection, and research purposes.Some of the sectors where X-rays are used include:
- Medicine: X-rays are widely used in radiology to diagnose a wide range of medical conditions. They can be used to identify bone fractures, detect lung diseases like pneumonia, examine internal organs, and detect pathologies like cancer.
- Dentistry: Dental X-rays, known as radiographs, are essential for diagnosing and monitoring dental conditions, such as cavities, infections, and orthodontic problems.
- Security and inspection: X-rays are used in airport security checks to inspect baggage and identify dangerous or illegal objects. They are also used to inspect containers in ports and customs for cargo trafficking.
- Industry: In industrial sectors, X-rays are used for non-destructive inspection of materials such as metals, plastics, and ceramics. This helps to detect defects or anomalies in products, ensuring quality and safety.
- Scientific research: X-rays are widely used in scientific research to study the structure of materials, crystals, and biomolecules. X-ray crystallography, for example, is fundamental for determining the three-dimensional structure of proteins and biological molecules.
- Archaeology: X-rays are used to examine ancient objects without damaging them. This technique is valuable for discovering hidden details or internal layers of archaeological objects.
- Aerospace: The aerospace industry uses X-rays to inspect critical components, such as welds and internal engine structures, to ensure the safety and reliability of spacecraft and aircraft.
- Oil and gas: X-rays are used to inspect pipelines and joints to detect any defects or corrosion, helping to prevent leaks and accidents.
- Geology: X-rays are used in geology to study the composition and structure of rocks and minerals, aiding in the search for natural resources and the study of the earth.
- Food industry: X-rays are used to inspect food products, for example to detect metal contamination or foreign bodies in packaged products.
These are just some of the sectors where X-rays are used for various purposes.X-ray technology continues to evolve and find new applications in various scientific and industrial fields.After 120 years of generating X-rays through thermionic emission with a filament, the near future presents a change that is taking its first steps in recent years:THE CARBON NANOTUBE (CNT) X-RAY TUBECarbon nanotube (CNT) X-ray tubes operate differently from traditional X-ray tubes. Instead of relying on thermionic emission, which uses a heated filament to generate electrons, CNT X-ray tubes utilize field emission.Field emission occurs when a strong electric field is applied to a metal surface, causing electrons to be emitted.This phenomenon can be observed in various applications, such as spark plugs, where a high voltage generates a brief, intense spark of electron current."Electric field"In any field emission, the electric field is intensified by reducing the aspect ratio of the metal surface; if the metal is sharp-pointed, the electric field is more intense and the sharper the tip, the more intense the field becomes.Carbon nanotubes (CNTs) are the ideal field emitters known to physics because they have an extremely sharp tip. CNTs are typically 10 nm wide but 20-50 μm long and have the same electrical properties as metal."Array CNT per la generazione di elettroni "Thanks to their excellent field emission properties, carbon nanotubes (CNTs) can generate extremely high electron currents.X-rays generated with carbon nanotubes (CNTs) exploit field emission to produce electrons, which are then accelerated towards a dense target material, typically tungsten, in order to generate X-rays, following the same principle as conventional X-ray tubes."a. Simplified diagram of a CNT X-ray generator"In the two images below, the design of a conventional X-ray tube is compared with that of a CNT X-ray tube.The basic structure of the two X-ray tubes is similar, and both have most of the same key components.X-ray tubes with carbon nanotubes (CNT) feature a distinctive structure around the cathode that contributes to stable and efficient control of electron emission. This characteristic is crucial for the operation of such X-ray tubes.
"Conventional X-ray tube" "X-ray tube with Carbon Nanotubes (CNT)""Conventional filament x-ray tube" "X-ray with CNT field emitters"The technology of field emission for X-rays (Field Emission X-Ray) using Carbon Nanotubes (CNT)has been considered an interesting alternative to thermionic emission for electron production in various devices, including displays, electron microscopes, and X-ray tubes.The behavior of these emitters is described by the Fowler-Nordheim equation, where the material should have a low extraction work and/or a high field enhancement factor to reduce the extraction field.These emitters, known as "cold cathodes," require only the application of moderate voltage to a nearby electrode, avoiding the high temperature needed for electron production in thermionic cathodes.The elimination of thermal management of the cathode is one of the main advantages of X-ray field emission over thermionic tubes, although in some cases, thermal energy is generated."Array group of field emitters"The produced thermal energy is primarily dissipated by heating the anode, remaining a limitation for both field emission and thermionic X-ray production.Another advantage of field emission X-rays is the ability to switch instantly from the cathode, and thus the X-ray beam, at speeds limited only by control electronics.This enables pulsing the beam at a high frequency and synchronizing it with physiological signals, challenging to achieve with thermionic sources that require a finite heating and cooling period.Research has been conducted on field emitters such as "metallic tip" and "Spindt" for X-ray generation, but material interactions, such as sputtering and degradation within the tube, have limited their use in medical imaging."Various types of field emitters"CNT X-ray Field Emission (Carbon Nanotube Field Emission X-Ray)The discovery of carbon nanotubes (CNT) by Sumio Iijima in 1991 sparked global interest in the synthesis and new applications of this unusual structure.CNTs, with their small diameter and relatively long length, exhibit a high aspect ratio and an atomically sharp tip.These characteristics give them a significant field enhancement factor when a voltage is applied, making them excellent field emitters.Initial research on field emission imaging with CNT cathodes showed promise, although results varied.Some studies revealed low current and short cathode lifespan due to issues such as poor adhesion, oxidation, and CNT film sputtering. Other studies demonstrated higher current and longer lifespan.Twenty years after these initial investigations, CNT cathodes are now capable of providing high current density and a lifespan comparable to conventional thermionic cathodes.Numerous academic and industrial research teams have dedicated themselves to developing this technology, but currently, no other nanomaterial has achieved the same current density, lifespan, and reliability as CNT cathodes.CNT X-ray Devices (Carbon Nanotube X-Ray Devices)CNT Cathode (Carbon Nanotube Cathode)The primary initial goal of designers was the development of robust CNT cathodes with high current density for X-ray production.Cathode prototypes have been created, and various deposition techniques have been explored, including screen printing, spin coating, direct CVD, and electrophoretic deposition (EPD).Although obtaining electrons from a carbon nanotube (CNT) cathode could be achieved in various ways, the performance varied significantly.To make these cathodes work well in medical imaging devices, it was necessary to enhance the materials and production methods of CNTs.The fabrication of CNTs, involving how they are made, their length, purity, and the presence of any foreign particles, has been crucial to achieving robust cathodes.A team from the University of North Carolina (UNC) perfected electrochemical deposition (EPD) techniques using few-walled CNTs created by a group from Duke University.In the process, alcohol-based solutions were used, supplemented with substances like magnesium chloride (MgCl2) and small glass particles as adhesives.Insulating materials like glass or quartz were patterned with areas where conductive material could be deposited using photolithography.EPD was employed to place the CNT-based material on the prepared support.Afterward, a substance called photoresist was removed, revealing the desired cathode pattern, although the CNT-based material did not adhere perfectly to the surface.Finally, the supports were heated to very high temperatures, melting the adhesive glass particles and creating a structure with CNTs partially connected at the ends.X-ray Source with Carbon Nanotube (CNT) Single BeamThe basic design of an X-ray source using single-beam field emission carbon nanotubes (CNTs) is similar to that of a conventional thermionic X-ray tube.A typical CNT source comprises a cathode, a grid extraction electrode known as the gate, a focusing structure, and a tungsten anode inside a vacuum container."X-ray Tube with Carbon Nanotubes (CNT)"Ensuring Durability and Advancements in Carbon Nanotube (CNT) X-ray Sources and to ensure the longevity of carbon nanotube (CNT) emitters used in X-ray sources and explore further possibilities, maintaining a high vacuum is crucial.CNTs are more vulnerable to oxidation than traditional tungsten filaments in conventional X-ray tubes.Typically, an active or passive pump is used based on the device's power.To generate X-rays, a positive voltage is applied to the anode in unipolar mode.Electrons are extracted from the cathode by applying voltage between the cathode and the gate, with most electrons passing through the gate and reaching the anode.The focusing lens shapes the electron beam before hitting the anode, ensuring the desired focal point size.An advantageous feature of these CNT sources is the ability to easily program and synchronize electron emission and X-ray pulses with external triggers, reducing blurring in images due to patient or animal movement during exams.Initially developed for preclinical imaging of small animals in biomedical research, these CNT sources have succeeded in performing high-resolution scans synchronized with breathing and heartbeat.However, a challenge in advancing this technology has been ensuring the power and stability required for long-term imaging applications, addressing issues related to CNT quality and initial voltage instability.Potentially, these CNT sources could also be used in non-destructive testing (NDT) and security applications.Significant progress has been made over the years to mitigate these challenges:
- Optimization of CNT raw material structure and morphology and CNT cathode design for both high current density and total emission current,
- Improvement in CNT source design and production processes,
- Integration of electronics to compensate and regulate X-ray photon flow.
While there is room for further improvement, current CNT X-ray sources can deliver the same power as conventional thermionic X-ray tubes, limited by anode thermal management rather than cathode emission current.An example of a high-power fixed-anode CNT X-ray source is shown in the figure below.The sealed source, without an external active ion pump, can operate at 120 kVp and 50 mA tube current with a variable focal point size.
"a. Simplified Diagram of a CNT X-ray Generator"Spatially Distributed Array of CNT X-ray SourcesA traditional thermionic X-ray tube is a single analog device that utilizes a single focal point on the anode to generate X-ray radiation.This design limits its capability to perform advanced imaging techniques, such as Computed Tomography (CT) and other forms of three-dimensional imaging, as it requires physically moving the X-ray source to different positions to collect projections from various angles.However, innovation has arrived with the introduction of a spatially distributed array of X-ray sources, each with multiple focal points distributed in space.This approach has brought significant improvements in spatial and temporal resolution, opening new possibilities in the field of medical imaging, Non-Destructive Testing (NDT), and security.
"CNT Arranged in a Circle for CT System" a. Single emitter in motion for Tomosynthesis b. Linear array of emitters with sequential activation"X-ray Field Emission Sources based on Carbon Nanotubes (CNTs) have played a crucial role in this innovation.Thanks to their relatively simple design and low thermal contribution, CNTs have enabled the construction of multiple spatially distributed arrays of sources with variable configurations to adapt to the system's needs.However, this new approach has posed some technical challenges, such as the need to ensure consistency among individual CNT cathodes in terms of field emission, focal point dimensions, and X-ray outputs.This is essential for achieving the quality of reconstructed images.Compared to a single-beam X-ray source, the distributed X-ray source array presents additional technological challenges, such as consistency in the field emission characteristics of individual CNT cathodes, focal point dimensions, and beam-to-beam X-ray outputs.For most imaging applications, X-ray dose and focal point size must be consistent from view to view to ensure the quality of reconstructed images.This becomes challenging when 10 to 102 CNT cathodes are used for each X-ray source array. The field emission current changes exponentially with the polarizing electric field.
“Array of emitters in line with sequential activation”Small variations in the composition, geometry, or morphology of the emitter can lead to significant differences in emission behavior among individual cathodes.Despite continuous improvements in manufacturing technology, some variations in the cathode are inevitable.To mitigate this issue, dedicated electronic devices have been developed to real-time compensate for variations in the emission behavior of individual cathodes and adjust the outgoing X-ray photon flow to achieve the coherence and reliability required for imaging."Control electronics for the multiple management of arrays"Today, arrays of spatially distributed CNT X-ray sources with various configurations and specific performances are commercially produced, based on technologies initially developed at the University of North Carolina (UNC).The figure below illustrates the functioning mechanism of the multi-source array.To showcase the capabilities of this technology, an array of CNT X-ray sources is shown, manufactured according to stringent specifications for a new TC system under development.
"Multiray array with 250 emitters" "a. Simplified diagram of multiple CNT X-ray generators "Multiray X-ray arrays represent a significant evolution in X-ray generation. These systems consist of 250 emitters, or focal points, each with a focal point size of approximately 1 mm x 1 mm, distributed over a length of about 100 cm.They are designed to operate at 180 kVp and 30 mA cathode current.This configuration enables the acquisition of high-resolution and precise radiographic images, making them ideal for advanced medical applications such as computed tomography (CT) and other three-dimensional imaging techniques.Example of a new system with nanotubes:"Stationary X-ray CT system with ECAC-certified nanotubes used to ensure the safety of our travels"Here is some key information about X-ray systems with nanotubes:
- Operating Principle: In an X-ray system with nanotubes, a voltage is applied to carbon nanotubes acting as cathodes. Electrons are emitted from the surface of the nanotubes when subjected to high voltage. These accelerated electrons strike an anodic target, often made of tungsten or other materials with high atomic density. The interaction of high-energy electrons with the anodic target produces X-rays.
- Advantages: X-ray sources with nanotubes offer several advantages over traditional hot cathode tubes used in radiology. These advantages include a more compact physical size, greater energy efficiency, the ability to quickly and precisely adjust X-ray intensity, and increased operational lifespan.
- Applications: X-ray systems with nanotubes are used in various applications, including medical radiology, dentistry, non-destructive inspection in industries, and advanced scientific research. They can be used for generating X-rays at low, medium, or high energy levels, depending on the application requirements.
- Radiation Exposure Reduction: Another advantage of nanotubes is the precise control of X-ray production, contributing to reducing patient exposure to radiation during diagnostic examinations.
- Technological Development: Carbon nanotube technology is constantly evolving, with efforts to further improve the performance and reliability of these X-ray sources.
However, it's important to note that despite the advantages, widespread adoption of X-ray sources with nanotubes may require significant investments and specific regulations to ensure safety and effectiveness in medical and industrial use.Research and development continue to make this technology more accessible and reliable.CONCLUSIONSThe field emission X-ray technology based on carbon nanotubes (CNT) offers distinct advantages over traditional thermionic X-ray tubes due to the field emission mechanism for electron generation, including electronic programmability of X-ray radiation and flexibility in manufacturing distributed X-ray source arrays with various configurations.These capabilities are particularly attractive for physiologically guided imaging and the design of tomographic imaging systems with improved resolution, mechanical robustness, and mobility.While demonstrating X-ray generation using CNT emitters is relatively straightforward, achieving the required power, stability, and reliability for clinical and industrial imaging has been challenging.Through improving the quality of CNT materials and advancements in the design and production of cathode structure and X-ray sources, the performance of CNT X-ray sources has made significant progress compared to reports from twenty years ago.CNT cathodes have demonstrated the ability to generate current and current density even for high-power medical CT tubes.Today, the power of commercially manufactured CNT X-ray sources is not limited by the capacity of CNT cathodes but by the thermal management of the anode, as in traditional thermionic X-ray tubes.Utilizing the capability of distributed X-ray source matrix to emit radiation from various viewing angles without any mechanical movement, several tomosynthesis imaging devices have been proposed and demonstrated for patient imaging studies in clinical applications, including breast cancer detection, diagnosis of various lung diseases, limb imaging, and dental examination.A mobile digital radiography device powered by CNT X-ray has received FDA approval in the United States and is now clinically utilized.Several tomographic imaging systems based on CNT X-ray source matrices are in regulatory approval. With ongoing progress in CNT X-ray source technology, new applications for medical imaging, non-destructive testing (NDT), airport security, the food industry, and potentially radiotherapy can be expected.Bibliography:
- Wang, X., Zhang, J., Wang, R., and Lu, J. (2002). Carbon nanotube-based field emission X-ray sources. Applied Physics Letters, 80(20), 3736-3738.
- Bronstein, Y., Lai, B., Chtcheprov, P., Zhao, Y., Iniewski, K., McCann, P., et al. (2009). Nanocoax-based field emission X-ray sources. Nanotechnology, 20(26), 265-703.
- Kim, J., Lee, S., Cho, J., Jeong, J., In, S., and Moon, E. (2011). Microfocus X-ray imaging of tumors in small animals using a carbon nanotube field emission micro-CT scanner. Radiology, 260(1), 265-270.
- Calderon-Colon, X., Geng, H., Gao, W., An, L., Cao, G., and Zhou, O. (2012). A carbon nanotube field emission cathode with high current density and long-term stability. Nanotechnology, 23(32), 325-707.
- Lai, B., Duan, X., Yuan, X., Wang, E., and Zhang, H. (2013). Design of a carbon nanotube-based gas-filled x-ray tube. Applied Physics Letters, 102(22), 223-503.
- Chen, H., Zhang, Y., Fu, K., Duan, X., Zhang, S., Cheng, Z., et al. (2015). Stationary scanning x-ray source based on carbon nanotube field emitters. Scientific Reports, 5, 16098.
- Lai, B., Chen, R., Zhang, Y., Gelman, A., Wu, H., and Liu, J. (2021). Advances in carbon nanotube X-ray devices for medical imaging applications. Medical Physics, 48(6), 3057-3074.
- De Volder, M.F.L., Tawfick, S.H., Baughman, R.H., and Hart, A.J. (2013). Carbon nanotubes: Present and future commercial applications. Science, 339(6119), 535-539.
- Harris, P.J.F. (2009). Carbon nanotube science: Synthesis, properties and applications. Cambridge: Cambridge University Press.
- Monthioux, M. and Kuznetsov, V.L. (2006). Who should be given the credit for the discovery of carbon nanotubes? Carbon, 44(9), 1621-1623.
The sources listed offer a robust foundation for the information presented and are accessible for thorough verification of the statements made in the text.The Evolution of Industrial Inspection from the Beginning to Today by Comet-YxlonComet-Yxlon's history in the field of X-ray industrial inspection began in 1895 when German physicist Wilhelm Conrad Röntgen discovered this revolutionary technology.Röntgen's discovery opened new possibilities in medical diagnosis and industrial inspection. However, in 1896, German entrepreneur Carl Heinrich Florenz Müller played a key role in developing the first X-ray tube, turning Röntgen's discovery into a practical application.In 1927, Müller's factory was acquired by Philips. A pivotal moment in Comet-Yxlon's history was its collaboration with Philips in 1998.During that period, Philips decided to focus primarily on the medical sector, separating from the industrial branch. This led to the creation of Yxlon International GmbH, specializing in industrial inspection using X-rays.The growth path didn't stop there. In 2007, Yxlon was acquired by the Comet Group, a global leader in manufacturing X-ray tubes in metal-ceramics.This union resulted in a merger with Fein Focus, previously acquired by Comet in 2004, strengthening Yxlon's position in X-ray inspection and computerized tomography (CT), significantly contributing to quality and safety in various industrial fields.In 2022, after 95 years of history, Yxlon International rebranded as Comet-Yxlon, maintaining its position as a pioneer and leader in industrial X-ray inspection.Until now, Comet-Yxlon has consistently focused on improving its tomography facilities. In the near future, there might even be the possibility of exploring applications involving innovative nanotube technology."Comet-Yxlon: Evolution of Industrial Inspection from the Beginning to Today"OUR FACILITIESIn today's industrial landscape, characterized by increasing global competition, the need to adopt innovative technologies to remain competitive is evident.In this context, X-ray computerized tomography stands out for its revolutionary potential, providing detailed information to explore defects and imperfections otherwise challenging to detect.This advanced analytical capability is paving the way for innovation and improvement in industrial design and production.Our range of Comet-Yxlon systems addresses these evolving needs, offering cutting-edge solutions for quality control and advanced analysis, crucial elements for excelling in the current competitive environment.We look to the future with confidence, recognizing that technological innovation is crucial to addressing today's challenges and seizing new opportunities for growth and development."Comet-Yxlon Micro-Tomography System"Xrayconsult is consistently ready to offer information regarding this technology. For a glimpse of our facilities, please click on the provided link: Tomografia Industriale